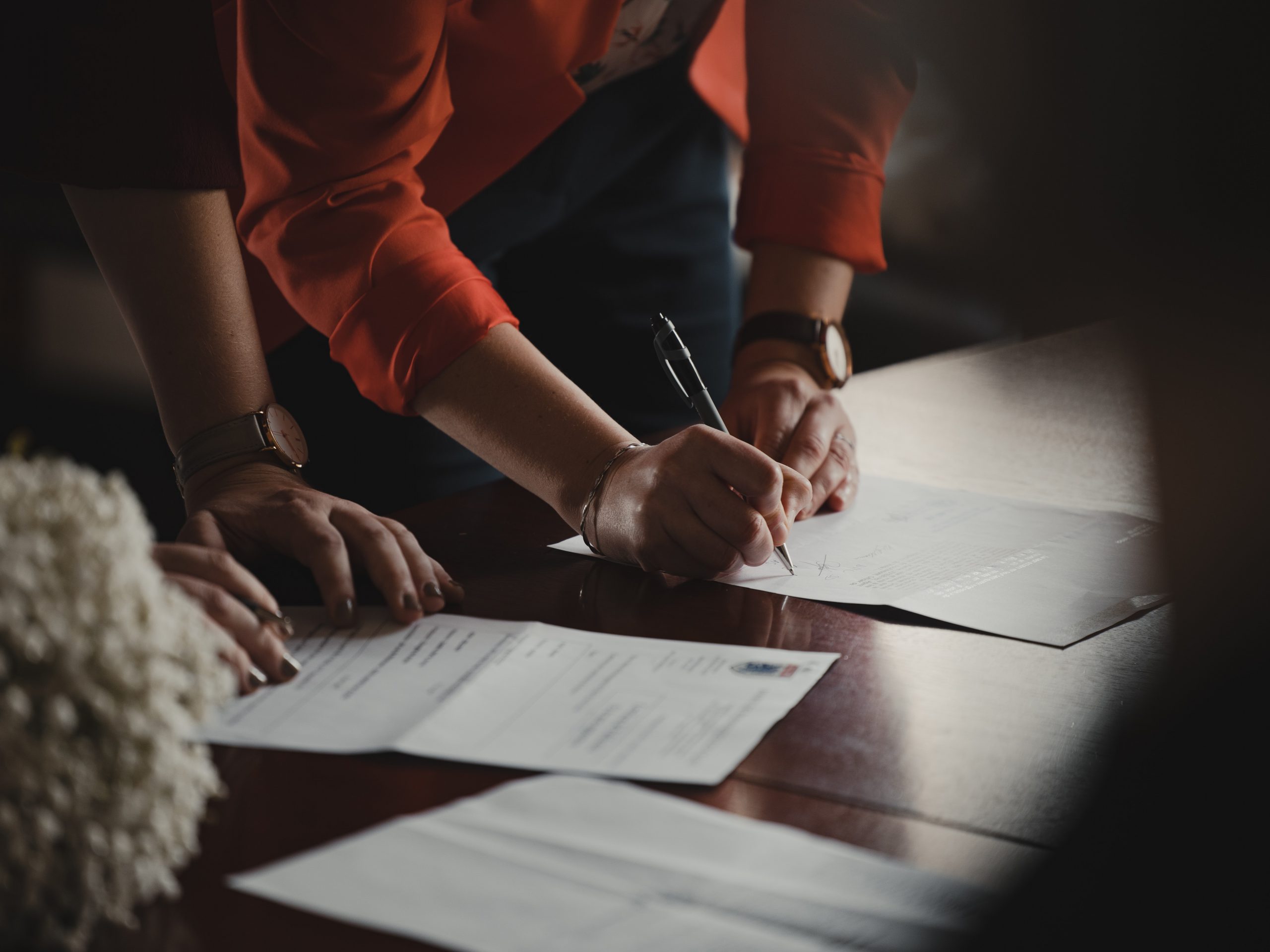
Raw material, ingredient and product data submission.
Onboarding is one of those buzzwords in the business world, and refers to what we used to call “setup.” But to its credit, the term really speaks to the effort and care we put into hoisting your designated kosher person on board with all they need to know. In this month’s post, we’re focusing on ingredient and product data submission.
It’s been almost a century in the making, but OK Kosher has a pretty streamlined system for collecting the ingredient and product data we need to certify companies as kosher.
That’s why we’re sharing with you – the kosher companies (and prospective kosher companies) – some essentials for a smooth and sound kosher certification onboarding.
This month, you’re in for a treat. A masterclass from one of our very own for the inside scoop on ingredient sourcing and submission for kosher certification. Devorah Weingarten, Senior New Accounts Specialist, has been with OK Kosher for 15 years. She’s even had a hand in shaping our policy for how we process companies from kosher hopefuls to vetted-and-certified companies (yes, she’s that pro).
So without further ado, let’s hear from Devorah.
Kosher Certainly: Hi Devorah, thanks for helping us out today!
Devorah: My pleasure!
KC: So, tell us your role in setting companies up for OK Kosher certification – their kosher onboarding.
DW: Sure. At the point when a company has applied for certification and accepted the terms, we start the data collection process. I give companies the instructions and, sort of, coach them on the right way submit data now, and for in the future.
KC: So what does that look like, typically?
DW: I explain the kosher onboarding process to their kosher contact person, and give them two things: a comprehensive document with our specifications, and a sample spreadsheet. The spreadsheet is a simple example of how we want their products, ingredients, vendor name and – if they have them – RMCs listed. So, my example products are Chocolate Cake, Vanilla Cake and Strawberry Cake. The spreadsheet shows how I want to see those product names listed, with the ingredients (let’s say those are flour, sugar, cocoa, etc.), any internal naming system they may have, and any accompanying kosher certifications that those ingredients have.
KC: Okay, okay, so it sounds like at this point in the kosher onboarding the company really needs to have their ducks in a row. They need their products and ingredients super organized from the get-go in order to send it in the right format.
DW: Correct. And it’s here where we sometimes find the mistakes start happening.
KC: Okay, what’s mistake #1?
Mistake #1: Don’t send us ingredients within ingredients, if your company isn’t the maker of that ingredient.
So for example: Let’s say chocolate chips are one of the ingredients you use in a product you make. As long as you bought those chocolate chips from an outside vendor, I don’t want you to send me the ingredients in them. If they come with a kosher certification we accept, then you’re good to go. That ingredient will be approved. Done, on to the next. If it doesn’t come with a kosher certification, or we don’t accept the one it does have, then it needs to be re-sourced.
KC: What you’re saying is that it saves everyone time by checking the existing kosher certification of an ingredient, rather than listing out all of the ingredients inside that ingredient. You’d be sending the contact person to track down the vendors of all those raw materials; sugar, cocoa butter, chocolate liqueur, vanilla flavor…etc. But that’s a tall task when you’re not the manufacturer. Right?
DW: Yes, but it goes much further than that. If the company at hand doesn’t make the chocolate chips in-house, but I’m under the impression they do (because the chocolate chips’ raw materials were submitted as ingredients), then I start approving those raw materials, but I’m skipping over the fact that those raw materials were combined, heated, and manufactured into a product – chocolate chips – in another factory that may not be kosher. Which means that, even if all the raw materials within it are approvable, the chocolate chips are not kosher! So we shouldn’t be approving it.
KC: Sounds like a potential mess!
DW: Yes. Luckily it’s never gotten to that point. We’ve never actually certified an ingredient like that when we weren’t supposed to. We have a solid system and strict QC measures in place during the kosher onboarding. So even if I or a member of our team were to miss that mistake, someone would catch it after me – the Account Rep, or someone in the Ingredient Approval department, the Rabbinic Coordinator, if it comes to it. But we don’t want to put our clients through that. It can put a major hold on certification, because we’d have to go back and correct the problem – we never let that sort of thing slide. Kosher without compromise!
KC: Indeed. So let’s back up a bit. You mentioned that if the company submits an ingredient that isn’t kosher certified, then OK Kosher rejects it, and it needs to be re-sourced. Is that across-the-board? And how does that work?
DW: Good question. First of all, we don’t always reject an ingredient for not having a kosher certification. We use something called the Kosher Group System. This is actually something that all major kosher certifiers use that helps streamline the approval process. There are Groups 1 through 6, with some sub-groups like 2A, but most are for our internal use only. What sometimes helps at this stage is Group 1. If an ingredient is a G1, it’s categorically accepted – in other words, it doesn’t need proof of certification. For instance, water is a G1. So is flour. Some raw vegetables and fruits, for example.
So when I receive an initial ingredient list from a company, then I can single out what I know to be G1’s, and auto-approve them. I can then pass on the shortened list to the ingredient approval department. They’ll come back to me with a list of anything that either wasn’t approved so needs replacing, or still needs proof of certification in the form of a kosher certificate. As an added QC measure, our data team will also scan for Group 1 ingredients, to further save the client time and effort.
If an ingredient is a G1, it’s categorically accepted – in other words, it doesn’t need proof of certification.
KC: So then how should a company go about replacing an ingredient? Is that tricky?
DW: Obviously, companies of different sizes and stages of growth have varying levels of experience with ingredient sourcing and R&D, trial runs, etc. So we try to help out where needed at this point in the kosher onboarding. A larger, more established company usually goes through suppliers. Those suppliers can help them find an alternate, or a different vendor for that ingredient. Those suppliers usually know the drill and have information like kosher certification on file for what they sell.
But for companies who could use some support, we have our own kosher ingredient and supplier database. It’s really one of the most extensive databases you’ll find in the kosher world. Also, our Rabbinic Coordinators have close relationships and a deep understanding of the facilities they certify. So I can reach out to them and say, for instance, Can you recommend a supplier for – erm – chocolate chips(!) in such-and-such size, that’s Pareve, and can fulfill this client? Again, it’s usually the applying company who searches out a replacement, but if needed, we can certainly help out.
For companies who could use some support [in re-sourcing an ingredient], we have our own ingredient and supplier database. It’s really one of the most extensive databases you’ll find in the kosher world.
KC: That’s why we call it Kosher Certainly!
DW: …Really?
KC: No, I just made that up. Anyway, Devorah, at this stage, is there anything else you just wish your clients knew?
DW: Well, yes.
Mistake #2: We know your company doesn’t make chocolate cake, vanilla cake or strawberry cake. (Devorah just likes cake). The spreadsheet is just an example.
Once, I sent a contact person my sample spreadsheet and he called me back saying, “Devorah, we’re quite shocked that you misunderstood our operation so majorly. I received your spreadsheet, but we do not produce chocolate cake, vanilla cake or strawberry cake. We don’t make cakes at all!”
KC: Oh my. I guess it’s worth addressing – and we can call it Mistake #2.
So then, when the company lists all the kosher certifications in the spreadsheet, how to you verify all that data?
DW: We need the actual kosher certificates to verify that. [Here’s what an OK Kosher certificate looks like. – KC] Kosher certificates are official, signed documents from the vendor’s kosher certifier – whether it be us (OK Kosher), or any other kosher certification agency – that verify the item at hand is indeed certified, that the certification is current (not expired), and refers to exactly the item we’re dealing with.
KC: What do you mean by that last part?
Mistake #3: Not all ascorbic acid is packaged equal. (Or chocolate chips, for that matter).
DW: It’s essential for kosher onboarding that the name of the ingredient you list on the spreadsheet clearly correlates to how it appears on the kosher certificate. It doesn’t need to match exactly, if your company uses internal names that are different (we call it CI for Client Ingredient, and MI for Master Ingredient in our system), that’s okay. We just need a clear key to match them up.
Sometimes you’ll see one ingredient per kosher certificate. Sometimes you’ll have a range of items on one certificate. In the latter case, it makes kosher onboarding MUCH easier for both of us when you can single out the ones you’re submitting for that product. Either by highlighting, circling, or otherwise marking the row where that item appears on the document. If there is an RMC, then that too.
In addition, the same ingredient in different packaging sizes, such as citric acid in 1lb bags vs. in 5lb bags, are considered two separate ingredients. So the kosher agency would certify them separately. So if you are ordering citric acid in 5lb bags to use as an ingredient, but the kosher certificate you send me is for the citric acid in a 1lb bag, even if it’s from the same vendor, you’ll need to get me that certificate for the 5lb bag to match up to your ingredient.
KC: Why is that, if it’s the same stuff inside?
DW: Several reasons. One is that the vendor of that citric acid may outsource their packaging to more than one facility, and one of them might not be certified. Or maybe they have a per-production based certification which only includes the citric acid packed in the 5lb bags, and not the 1lb bags. Similarly; if one of the sizes becomes discontinued, we’ll know about it sooner by having that information on file. If we’re not monitoring that exact ingredient first-hand, anything can happen that may jeopardize the certification. The recordkeeping needs to be precise. Plus, when I send those ingredients to the data processing department to finalize, the naming needs to match what the field rabbi will see when he eventually drops in to inspect the facility. Otherwise the Rabbinic Coordinator would need to figure out next steps.
KC: Would that potentially hold up a production, in that case? Until we fully approve all the ingredients in the plant?
DW: Possibly. Every operation and ingredient is different, so it really depends. But suffice to say that all this precision is to prevent holdups, time-wasting, and interruption to production.
KC: I’m sure time is an important factor for companies.
DW: Definitely.
KC: Do you have any other tips for streamlining this leg of the kosher onboarding process?
Mistake #4: Don’t put off gathering kosher certificates ‘til the last minute.
DW: Yes. The more kosher certificates you can track down ahead of time – even if you can collect them before applying – the better. That can be the most time-consuming part of kosher onboarding, so doing it early is key. Our ingredient review department reviews every single certificate. That means that if we have to wait in the middle for the company to catch up and fetch more, then there’s a hold-up. One of the most common questions we get from companies applying for certification is how long it will take to get their certificates. But you’d be surprised at how many of those same companies in a rush also don’t get their certificates in order ahead-of-time! So that’s one of my most valuable pieces of time-saving advice.
You’d be surprised at how many companies in a rush also don’t get their certificates in order ahead-of-time!
KC: And supposing that a company does have all their certificates ready, is the ingredient review department quick with what they do?
DW: Well…yes, if many of the ingredients and certifiers are in our system, then absolutely, we can potentially approve or reject everything within a day or two. But we’re dealing with a unique product each time. So if we come across an unfamiliar ingredient or a certifier, that team will do their research to look into it.
That’s something the OK is really great at, actually. We go the full mile in trying to approve something. We don’t just reject it because it’s easier for us. As long as we can find out the needed information, and the item really is up to our standards, if we can approve it, we’ll approve it. It just may take some time for ingredients that are rarer, or for extra-long lists of ingredients we need to sift through.
KC: I guess that strengthens your point about having certificates at the ready, even more.
DW: Correct, that’s why that helps.
KC: You also mentioned that the ingredient review department looks at each and every kosher certificate to see if they can approve the ingredient. I know we’re in close contact with all the major kosher certifiers out there, and the OK team is familiar with their standards. So why isn’t there an across-the-board approval or disapproval for any one kosher certifier?
DW: This is something companies ask me a lot in the onboarding stage. Frequently, a company will ask me: Do you accept ABC or XYZ Kosher certifier? I tell them the same answer every time. That it depends on the product. You’re submitting chocolate chips with one certification, and then dried figs with the same certification? You might get one approval and one rejection. Kosher standards are dynamic depending on the food and the agency certifying it.
Kosher standards are dynamic depending on the food and the agency certifying it.
KC: Would you say that OK Kosher rejects more ingredients than others do?
DW: Yes, we probably do. OK Kosher really does have the highest standards out there. So you may see us reject some ingredients on basis of their certificate or just the type of ingredient it is. It doesn’t mean that the other kosher certifiers aren’t legitimate. It’s that, within the range of kosher standards, and we keep to the top level. And the kosher consumer knows our symbol represents that level of excellence.
KC: I know a lot of people ask why different kosher certifiers have different standards when we’re all supposedly following the same laws. But it’s a complex body of laws developed over a very long time. Kosher spans several different communities and sub-communities, who customarily follow different interpretations of that same law.
DW: Exactly. Many companies I hear from are confused about that. We reject a certificate and they say, What do you mean? It’s kosher! I explain that there are actually thousands of kosher certifiers out there. The major ones are usually transparent about their standards, so we have an idea of what we’re working with. But there are plenty that we simply can’t verify.
KC: I’m going to shift gears now. For companies developing a new product, it must be daunting – researching, prototyping, testing – all before knowing if we’ll even accept all the ingredients. Can they, hypothetically, give you a list of ingredients they’re thinking of using, and ask us to review them ahead of time?
DW: I do get that question sometimes. If it’s one or two items and the answer is at our fingertips, we’ll do that for them. For instance, we know that collagen and gelatin are tricky ingredients. We only accept a couple of vendors, and everything else, we reject. But for an entire product formulation – a whole list of ingredients and vendors – we can review it, but we just charge a processing fee. It’s the same fee they’d pay later on anyway, just up-front. And we put it towards your first year’s annual fee, so there’s really nothing to lose.
KC: What would you say to someone who’s reading this and thinking “Wow, kosher is really a time investment, in addition to a financial one.”?
DW: Well, that’s true. It’s an investment. Ordering needs to adhere to the ground rules for ingredients, but when the rabbi visits, there is also a procedure to adhere to there as well. But that said… ingredient approval really only needs to happen this way one time – during the kosher onboarding. Once they’re fully certified, we give each company their own account rep, who will train the company contact on our client portal. From then on, whenever there’s a new ingredient or product, they can just upload that data on the portal and everything gets approved digitally. Our rabbis still review each item, but you’ll only have to go back and forth with someone if there is some sort of issue. It’s really very streamlined.
KC: That sounds great. So then, what else does the company need to know for their certification, moving forward?
Mistake #5: Don’t even order ingredients before they’re approved for kosher.
DW: Well, when they do that – when a new product is in the works, the ingredients need approval before purchasing. Remember, once a company gets certified, the Mashgiach (field rep) visits the facility periodically, unannounced. If he finds unapproved or unlisted ingredients there, it may not be allowed in the facility according to their contract! And if that ingredient actually goes into a product run without approval and goes to market, we may need to issue a recall, which could cost the company money due to lost product and sales. If they need any guidance with this, they can just reach out to their account rep.
KC: That’s important to know! What mistake are we up to now…was that #5?
DW: There’s more where that came from. It’s also important to note some things that sometimes happen in the supply chain that can invalidate an approval.
KC: Sounds juicy. Like what?
Mistake #6: Don’t submit a kosher certification that’s been tampered with.
DW: Sometimes during kosher onboarding, a vendor gives you an ingredient that comes in bulk. But they repack it in their own warehouse, and label it with their brand. Our company contact asks them for a certificate, but the vendor name on the certificate doesn’t match the package, or has been crossed out because they don’t want to reveal who their supplier is. We consider that certificate to be invalid. One of our RC’s always used to say “Kosher certificates needs is like a passport!”
KC: But if the ingredient is exactly what they say it is, and the original supplier is acceptably certified kosher, then what’s the problem?
DW: For kosher certification purposes, repacking is a form of processing. In fact, any repack or relabel would cause the item to require its own kosher certification. Then the certificate from the original supplier is no longer valid.
KC: Makes sense.
Well! Thanks so much, Devorah, for running through all of these steps and possible pitfalls with us. I think this will really help companies set themselves up for success in getting certified during the kosher onboarding phase!
Close the hatch, you’re officially on board.
So there you have it. Six pearls of wisdom to abide by in onboarding your company with OK Kosher. Think it sounds complex? That’s why we dedicate so much attention to detail. And we’re always innovating new ways to save you time, energy and money, while keeping kosher without compromise. Stay tuned in for more insider information to help your company thrive with kosher.
The information presented in this blog post is based on research, general knowledge, and/or the author’s understanding of the subject matter. This blog is provided for informational purposes only and should not be relied upon by the reader or considered as professional advice. For specific guidance on any given topic, the reader should consult a qualified professional in the given field. OK KOSHER DISCLAIMS ANY LIABILITY FOR ANY LOSS OR DAMAGES RESULTING FROM RELIANCE ON THE INFORMATION PROVIDED IN THIS ARTICLE.